Finger-joint design and assembly technology for your hardwood trailer floors
The Zig-Zag joint is Prolam’s innovative alternative to the conventional hook joint used in the manufacturing of dry van hardwood floors since the beginning of the 20th century. Conventional hook joints are known to break with time and pressure, which means trailer floors need regular maintenance, repairs and even replacements much more often than the rest of the van. Zig-Zag were engineered with longevity in mind, making them key features to our hardwood floors.
Zig-Zag are finger-joints that fit together in a double-knuckle pattern. When assembled, the pattern ensures that pressure can be applied to slats on both sides of the joint, without compromising the glue line—or the structural integrity of the floor. This ingenious design makes our laminated hardwood floors much more structurally sound, resistant and durable than current products on the market.
Rely on Zig-Zag joints
for maximum durability.
How are our hardwood floors made
The Zig-Zag joint and assembly technology is standard on all Prolam floors, allowing them to withstand even the harshest conditions. First, our team sources high-quality wood from the best sawmills in North America. Wood planks are dried, sanded and rip-cut. A Zig-Zag crosscut is made to the ends of each slat in a precise finger-joint design, which ensures all ends will fit into each other. The slats are assembled and then glued together. Rigorous quality control checks are made throughout the manufacturing process so that you gain peace of mind knowing you are getting the best trailer floors for your fleet.
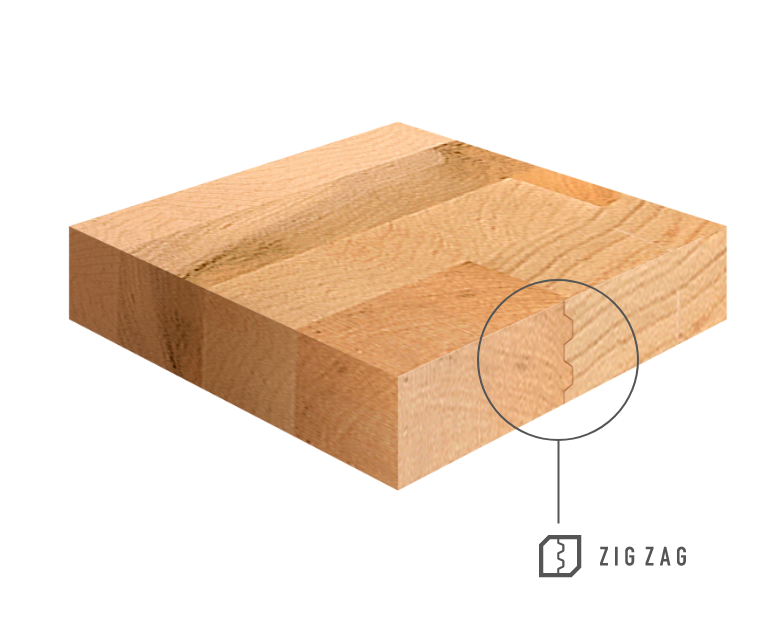
How it works for you
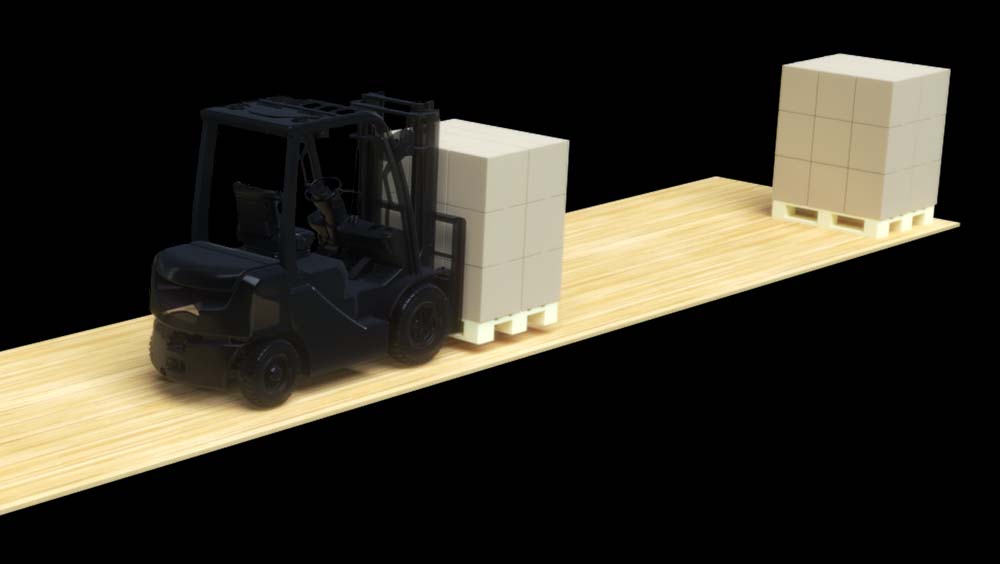
Greater fatigue resistance
Years ago, our R&D team made the choice of going forward with the development of a new finger-joint assembly that used a double-knuckle pattern. While most manufacturers are content to simply use the same pattern that was initially developed in the 1900s and glue the wood components together, Prolam’s unique technology leverages the mechanical characteristics of the wood so that forklift loads can be evenly distributed along the slats, creating a greater fatigue resistance and increased floor longevity.
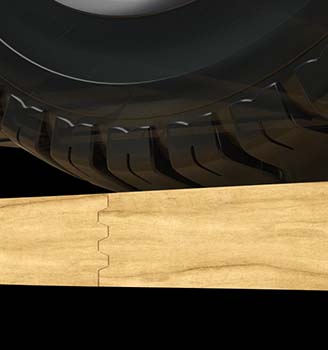
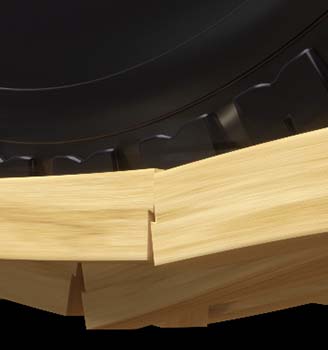
Less breakage
Rigorous lab tests prove that our joints can resist two times more the amount of stress than conventional hook joints. Hook joints resist pressure of 830 lbs/in2 before joint failure. Our Zig-Zag joints resist up to 1,500 lbs/in2. With about 2,000 joints per floor, get the strongest product with Prolam.
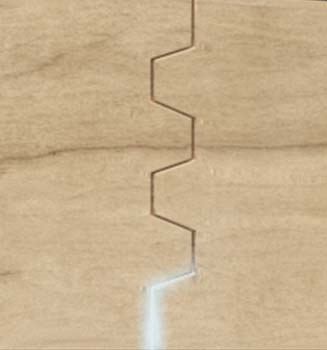
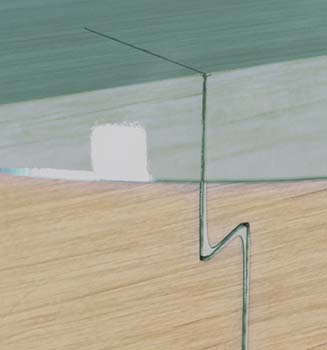
Less water penetration
With time and use, pressure applied to conventional floors will break the glue lines of hook joints. As water sprays towards unprotected joints, water will seep more quickly into the floors through capillary action than with Zig-Zag.
Water penetration might cause slats to absorb moisture easier, making them prone to swelling, which will eventually weaken the wood. The surface of the hardwood will be susceptible to more damages caused by regular wear and tear, reducing the floors longevity. The water could travel along the surface of the floors and damage goods.
Why take the chance?
Get the safest option with Zig-Zag.