An undercoating to fight moisture and the elements
Prolam’s P.U.R solution provides never-before-seen protection for hardwood trailer floors. The hot-melt polyurethane undercoating is applied on the undersides of laminated trailer floors. It eliminates the degradation issues associated with traditional water-based paint coatings. With P.U.R, your trailer floor can withstand water, sleet, snow, chemicals, and road debris. P.U.R is 11-times more abrasion-resistant than a water-based undercoating. P.U.R acts as a barrier between the hardwood floor and the outside world to ensure extensive protection and a long service life.
If the longevity of your trailer floor is a concern to you, look no longer.
P.U.R is the solution.
How it’s made
All P.U.R trailer floors are made out of our Zig-Zag joint design and assembly technology. Our team then applies P.U.R, a proprietary hot-melt polyurethane mixture, to the underside of the planks. As the polyurethane cools down, it forms a solid bond to the laminated hardwood fibers. P.U.R can be applied to targeted areas of the dry van’s floor’s underside, depending on your needs: it can be added to the rear and front wheels area only, the rear and front sections, or the complete underside surface.
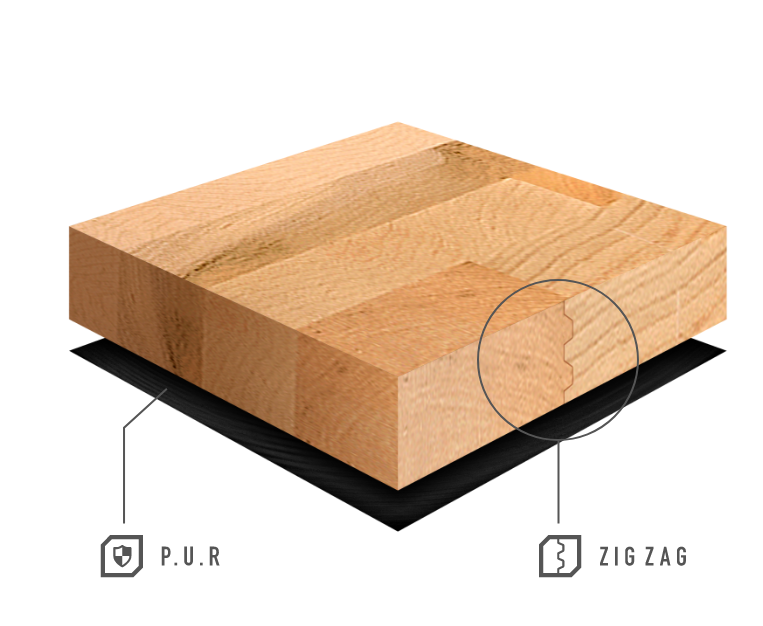
How it works for you
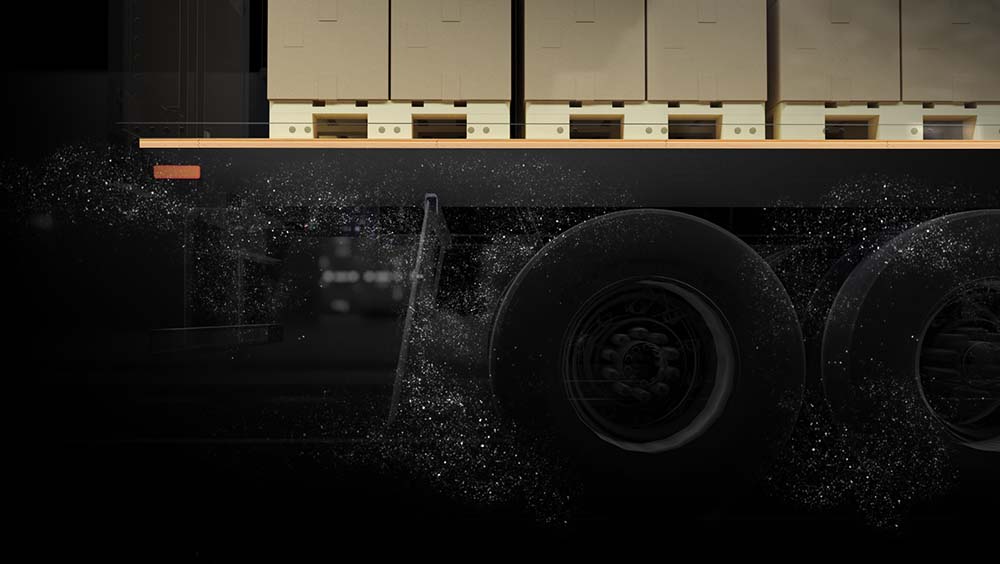
Highly superior abrasion resistance
Especially in climates with extreme weather conditions, water-based paint systems currently used to protect the underside of trailer floors can break down when subjected to intense water spray and road debris. This is especially true of specific areas, such as over the trailer wheels, which are constantly exposed to the elements.
In sandblast tests, our R&D team calculated the number of cycles needed for products to withstand sandblasting. The water-based undercoating only resisted 20 cycles—while P.U.R resisted 225 cycles, which is 11 times more resistant. Superior resistance means less maintenance and longer service life. Why choose anything else than P.U.R?
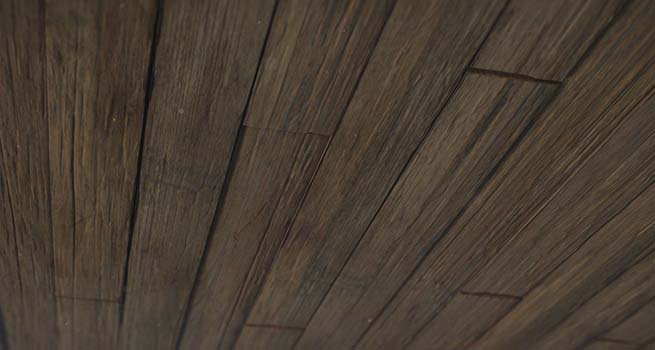
Reduced water damage
Since P.U.R has a greater abrasion resistance than any water-based undercoating and perfectly adheres to the hardwood fibers once applied, it also creates a much more resistant water protection than water-based undercoatings. Once water-based paint breaks down, the wood absorbs moisture, causing warping, swelling and deterioration of glue bonds at the joints. P.U.R mitigates issues with wood defects, knots and critical areas, such as butt-end joints, providing a single uniform barrier against moisture penetration at the underside of the trailer floor.
In a 24-hour exposure to water test¬, P.U.R has more than 8 times less absorption than water-based undercoatings. While water-based undercoatings absorbed 29.9 grams of water per 100 square inch, P.U.R only absorbed 3.4 grams/100 square inch. Once the undercoating has been breached, water can migrate into the trailer itself, resulting in severe cargo damage.
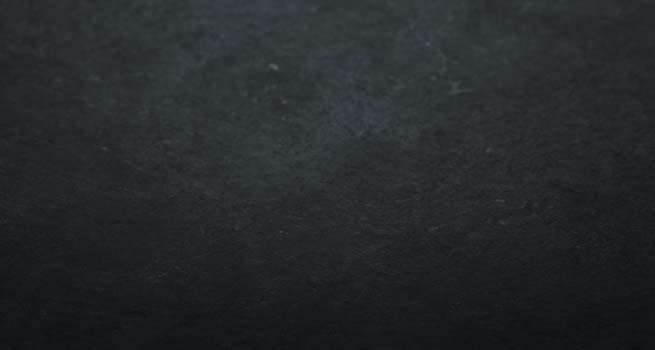
Greater return on investment
With superior abrasion resistance and reduced water damage to the undercoating and hardwood, P.U.R enables fleet owners to reduce the costs of frequent maintenance to the trailer floors. With better resistance to damage also comes either a greater service life or a higher resale value. All in all, P.U.R has a better return on investment than any other water-based undercoatings.
Choose the intelligent solution to protect your dry van floors. Choose P.U.R for your fleet.